Revolutionizing the Prototyping Process
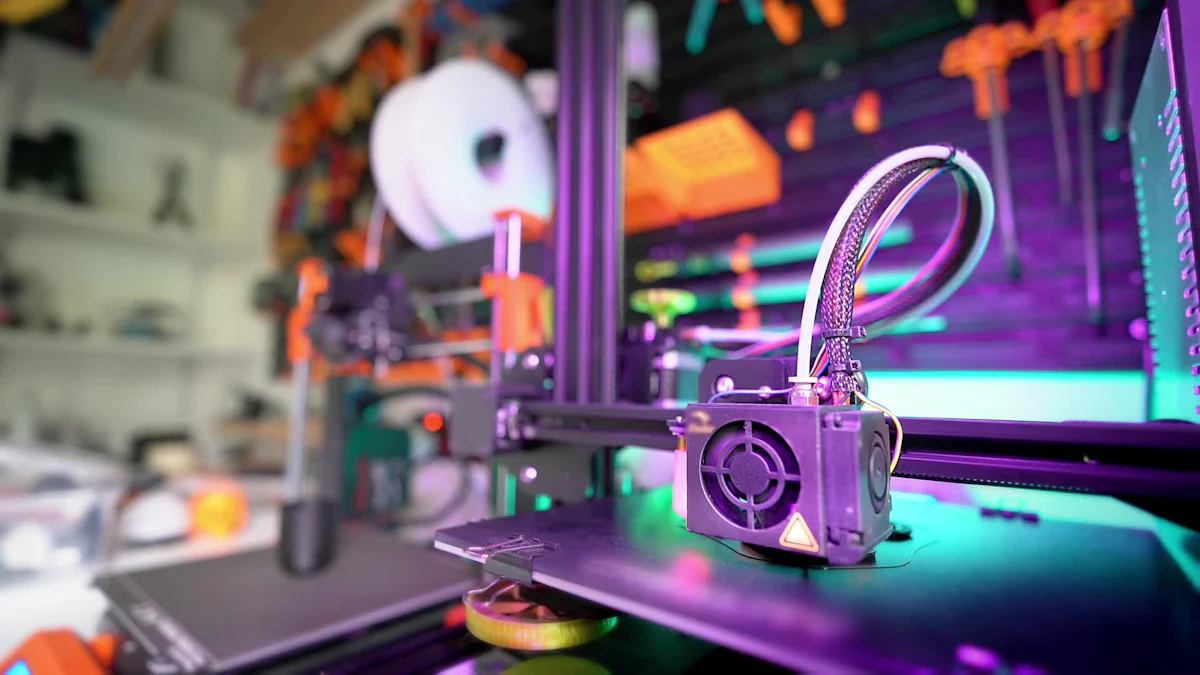
Rapid Prototyping
Speed and Efficiency
3D printing technology accelerates the prototyping process in the automotive industry. Traditional methods often involve lengthy and complex procedures. 3D printing, however, allows for the rapid creation of prototypes directly from digital designs. This speed enables automotive designers to quickly test and refine their ideas. The ability to produce prototypes in a matter of hours or days rather than weeks significantly enhances project timelines.
Cost Reduction
Cost efficiency represents another significant advantage of 3D printing in prototyping. Traditional prototyping methods can be expensive due to the need for specialized tooling and molds. 3D printing eliminates these requirements, resulting in substantial cost savings. The reduction in material waste also contributes to lower overall expenses. By minimizing both production time and costs, 3D printing makes the prototyping process more accessible and sustainable.
Iterative Design
Flexibility in Design Changes
The iterative nature of design benefits greatly from 3D printing technology. Automotive designers can easily make adjustments to their digital models and print new versions without significant delays. This flexibility encourages experimentation and innovation. Designers can explore multiple design options and optimize their creations based on real-time feedback. The ability to quickly iterate on designs leads to better-performing and more refined products.
Real-World Testing
3D printing facilitates real-world testing of prototypes, which is crucial for validating design concepts. Automotive engineers can create functional prototypes that closely mimic the final product. These prototypes can undergo rigorous testing under various conditions to assess performance and durability. The insights gained from real-world testing help identify potential issues early in the development process. This proactive approach ensures that the final product meets high standards of quality and reliability.
Applications in Automotive Interior Trim
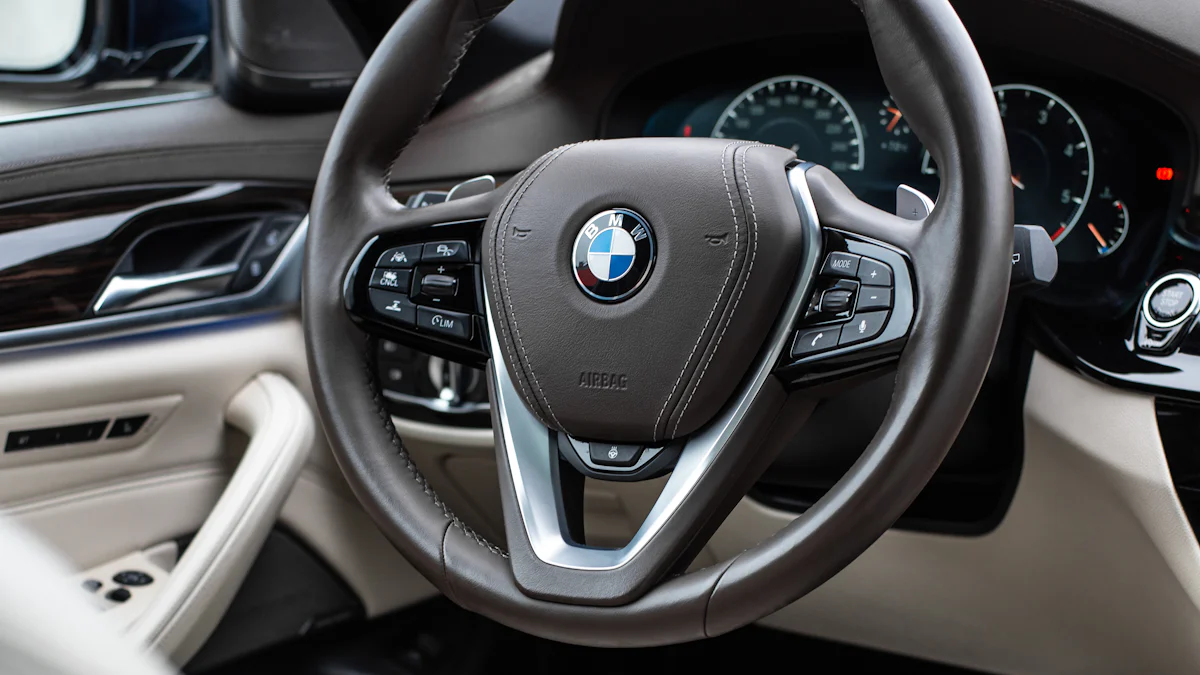
Customization in Automotive Interior Trim
Tailored Designs
3D printing technology enables the creation of tailored designs in automotive interior trim. Manufacturers can produce custom-designed interior panels and bespoke exterior trims that perfectly match individual customer preferences. This level of customization allows for the development of visually appealing components that meet exact specifications. For example, 3D printing can create unique dashboard designs and ergonomic seat structures that enhance both aesthetics and comfort.
Personalized Features
Personalized features represent another significant advantage of 3D printing in automotive interior trim. The technology allows for the creation of in-car accessories that reflect individual tastes. Customers can choose from a wide range of options to personalize their vehicles. This includes custom gear knobs, door handles, and other interior elements. The ability to offer such personalized features enhances customer satisfaction and adds value to the vehicle.
Design Freedom in Automotive Interior Trim
Complex Geometries
3D printing provides unparalleled design freedom, allowing for the creation of complex geometries in automotive interior trim. Traditional manufacturing methods often struggle with intricate shapes and detailed patterns. However, 3D printing can easily produce parts with complex angles and dimensions. This capability enables automotive designers to explore innovative designs that were previously impossible to achieve. The result is a more dynamic and visually striking interior.
Innovative Aesthetics
Innovative aesthetics become achievable through 3D printing technology. Designers can experiment with new textures, patterns, and finishes that enhance the overall look of the vehicle’s interior. The use of advanced materials like Polyamide (PA) and Acrylonitrile Butadiene Styrene (ABS) further expands the possibilities. These materials allow for the production of parts with unique visual and tactile qualities. The ability to innovate in terms of aesthetics sets 3D printed automotive interior trim apart from traditional options.
Material Versatility in Automotive Interior Trim
Use of Various Materials
The versatility of materials available for 3D printing significantly benefits automotive interior trim. Additive manufacturing offers a wide range of materials suitable for different interior car parts. Polyamide (PA) can be used for door handles and gear knobs, while Acrylonitrile Butadiene Styrene (ABS) is ideal for instrument panels and door trims. The technology has also advanced to produce parts with textures and patterns using 3D printed fabric. This material versatility ensures that each component meets specific functional and aesthetic requirements.
Sustainable Options
Sustainability represents an important consideration in modern automotive manufacturing. 3D printing supports this goal by offering sustainable material options. For instance, manufacturers can use recycled plastics and other eco-friendly materials to produce interior trim components. This approach reduces waste and minimizes the environmental impact of production. The ability to incorporate sustainable materials aligns with the growing demand for environmentally responsible automotive solutions.
Impact on Production Scalability and Cost-Effectiveness
Efficient Production
Scaling Up Production
3D printing technology enhances production scalability in the automotive industry. Traditional manufacturing methods often require extensive setup times and specialized tooling. 3D printing eliminates these constraints, allowing manufacturers to scale up production quickly. Automotive companies can produce large quantities of interior trim components without significant delays. This capability ensures that production meets market demand efficiently.
Reducing Waste
Reducing waste represents a critical advantage of 3D printing. Traditional manufacturing processes often generate substantial material waste due to cutting and shaping techniques. 3D printing, however, builds components layer by layer, using only the necessary amount of material. This method minimizes waste and reduces the environmental impact of production. The ability to create parts with minimal waste aligns with sustainable manufacturing practices.
Cost-Effective Manufacturing
Lower Material Costs
3D printing offers significant cost savings in material usage. Traditional manufacturing often involves expensive materials and complex supply chains. 3D printing uses a variety of cost-effective materials, including polymers and composites. These materials provide the necessary strength and durability for automotive interior trim. Lower material costs make 3D printing an attractive option for automotive manufacturers looking to reduce expenses.
Reduced Labor Costs
Labor costs decrease significantly with the use of 3D printing. Traditional manufacturing requires skilled labor for tasks such as machining, assembly, and quality control. 3D printing automates many of these processes, reducing the need for manual intervention. The technology allows for the production of complex parts with minimal human oversight. This automation leads to lower labor costs and increased production efficiency.
3D printing has significantly impacted the automotive industry, particularly in the realm of automotive interior trim. The technology has revolutionized prototyping by enhancing speed, efficiency, and cost reduction. Customization, design freedom, and material versatility have allowed for tailored designs and innovative aesthetics. Production scalability and cost-effectiveness have further solidified 3D printing’s role in automotive manufacturing.
The future potential of 3D printing in automotive interior design remains promising. Innovations in materials and techniques will continue to drive advancements in design, performance, and sustainability. The integration of 3D printing will streamline product development and foster further transformation in the industry.
Post time: Aug-01-2024